
JohnsByrne’s Jack Gustafson (COO) and Corey Gustafson (President) pose with Eagle President Mike King by the new cold foil system.
NILES, Ill. - April 24, 2018 - Luxury packaging printer JohnsByrne has installed the Eagle Systems Cold Foil system to better serve their client base and increase their ability to innovate. Founded in 1959, the organization remains a family-owned operation, with founder, John B. Gustafson’s four sons: Corey, Jack, Mike and Pate, running the business as President, COO and Executive Vice Presidents, respectively.
“We are a very client-centric, customer-focused operation,” said Corey Gustafson. “We look at the marketplace, and look for ways to provide solutions to problems our customers are having, and new ways to enhance their current product lines. We try to be very proactive about getting in front of our clients’ needs and the available technology, and the Eagle Systems Cold Foil system proved to be a great compliment to our offering; it was the right fit, at the right time.”
He noted that while they have, and continue to offer, hot stamping technologies, there were some applications where that process wasn’t a perfect fit. They could find a way to get it done, but Cold Foil, said Corey Gustafson, “gives us a great deal of flexibility, now, and nuance to our offerings. We can provide different solutions to the same problem, to find the one that best suits the project, product and customer. It’s a different tool in our belt.”
One of the differences they have found is that the Eagle Systems Cold Foil lays down gradation that is not able to be produced with hot foil stamping. “We’re now able to produce halftone gradation similar to that in a printing process,” said Corey Gustafson. “Talk about solving problems. Also, when we don’t have to take that extra step of off-press stamping, we’re able to save a pass or process — we can run it once, and we’re done at press speeds of 15,000 impressions per hour. It’s innovative, and it saves time and money on those jobs.”
The Eagle Systems Cold Foil system is a module that can be installed on most lithographic offset presses. The foil is applied in-line as the job is being run, and can be done by changing a single plate on the press before the run starts, allowing shops the flexibility of printing as normal or printing with in-line foil as needed. Foil is applied using a two-step process, both done in-line on the press. The first is to apply the adhesive to the substrate, using one of the printing units on the press, in register. Second, the foil carrier and substrate are pressed together, and where there is adhesive, the foil will release onto the substrate.
“I’ve seen a rise in cold foil in recent years,” said Mike King, President, Eagle Systems. “The applications are limited only to the printers’ imagination, and for JohnsByrne in particular, I am excited to see where they take it. It offers them a new, innovative option they can bring to their high-end customers, and gives them the ability to say ‘yes’ to more projects, with less time and money required to make it happen. We are excited to work with them, and we are looking forward to watching where they take this technology well into the future.”
The preceding press release was provided by a company unaffiliated with Printing Impressions. The views expressed within do not directly reflect the thoughts or opinions of Printing Impressions.
- Companies:
- Eagle Systems
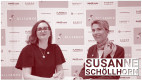




