By Erik Cagle
Senior Editor
There are enough headaches encountered between the time a customer's files are uploaded to your FTP site and when the truck rolls away from the back dock with finished product. But, while certain aspects of the workflow are tedious and time consuming, your perfect binder shouldn't be an attention, or time, burglar.
Most manufacturers of floor-model adhesive binders agree that time is of the essence. And the position of bindery operator often sees high turnover, making it imperative that a quality machine is easy to makeready, simple to operate, and equally user-friendly and fast on changeovers.
Shrinking Setup
As run lengths decline, setup time takes on even greater significance in terms of total job time, according to Don Dubuque, marketing manager for Standard Finishing Systems. This, in turn, mushrooms the labor cost per unit produced.
"An intelligent, intuitive, automated system lets even low-skilled operators build quality books, which is important as the pool of skilled operators continues to shrink," Dubuque states. "Printers and trade binderies need quick, efficient changeovers between different book sizes—without any compromise in quality or production speed—to ensure profitable book binding. As the market changes, some printers have discovered that it can be cost-effective and profitable to have direct in-house control of the total job, including waste, book quality and turnaround."
Standard Horizon's latest offering is the CABS 5000 perfect binding system, which includes gathering stations, 15-clamp perfect binder and three-knife trimmer. Up to six gatherers can be combined for a total of 36 gathering stations, which can feed single sheets or folded signatures up to 30 pages. It has a maximum cycle of 5,200 books per hour.
The Standard Horizon BQ-270 perfect binder can produce up to 500 books per hour. Features include touchscreen programming, 20 job storage memory capacity, and automated in-line cover scoring. Books up to 2˝ thick can be bound and up to 3.1˝ of cover stock can be loaded into the suction-fed cover station.
Cold- and hot-melt gluing capabilities are important to customers, according to Mark Pellman, marketing manager for Baum Corp. "This allows a wider variety of stocks to produce books and can affect the lay-flat conditions for a more functionable book to the reader," he explains.
Baum included both gluing methods in its Baumbinder 300 and 1500 perfect binders. The new 1500 has a top operating speed of 1,500 cycles per hour and can handle a maximum thickness of 50mm. Special features include double-capacity suction bag and suction hood. The 300 binds books, manuals, reports, etc., from 11x17˝ to 4x6˝ and up to 1.58˝ thick.
Automation is the name of the game when it comes to perfect binding, according to David Spiel, co-owner of Spiel Associates. "There is a lack of quality operators; they're getting harder and harder to find," Spiel points out.
The fully-automated Sterling Digibinder from Spiel Associates, which can bind 360 books per hour up to 11⁄2˝ thick, addresses this issue. The pneumatic clamp adjusts for book thickness automatically when the book size is keyed in. The unique roughing blade roughs the entire backbone of the book as opposed to notching. Twin glue rollers are said to ensure an even application and the Digibinder's nipper adjusts for the book thickness automatically. The machine includes a compressor.
Manufacturing equipment that can be quickly and easily set up, operated and maintained is the primary goal for Heidelberg USA, according to Steve Calov, product manager for stitching and perfect binding equipment. To that end, Heidelberg has developed the Quickbinder QB200 with touchscreen user interface to assist in the makeready and production of books.
Ironing Out the Front End
The QB200 features a 10-step job setup screen to ensure a smooth front end process. The standard automatic fault indicator helps recognize setup or operational problems.
"In the past, we had more mechanical movements of components that had to be adjusted by hand during the makeready process," Calov explains. "For instance, the glue pot had a series of cams that required adjustment for the glue spine length. Today, we have a sensor that reads the spine length of the book and automatically adjusts the glue setting in the glue pot. If any adjustments need to be corrected, we can accomplish this on the touchscreen."
The QB200 comes with three counter modes and four modes for machine operation: perfect bound, drawn-on cover, pad and pad/no cover.
Remote Repairs
Along with quick makereadies, automation and return on investment, good serviceability is a hallmark of quality adhesive binders, says Kerry Burroughs, manager of the perfect binding division for Muller Martini. "Many printers and trade binders are asking that their systems be modem equipped to facilitate remote diagnostics," he states. "That sharply reduces the need for service calls and all the time and expense that goes with them."
The Acoro perfect binder from Muller Martini is available in two models, with the A5 producing up to 5,000 books per hour and the AcoroPlus A7 has a top speed of 7,000 books per hour. It features the automatic makeready system AMRYS, which saves on time and doesn't require highly skilled operators to work the AcoroPlus. The automatic self-adjusting caliber (ASAC) compresses the job-to-job cycle with self-setting book thickness values.
Shorter runs equal more jobs and a need to keep moving product through in an expedient manner, states Jose Alvarez, marketing manager for Duplo USA. "Because printers are constantly printing short runs with more jobs, they need perfect binders that are equipped for short-run work, which demands quick setup and changeover," he says.
The Duplo MR 500 addresses this need. With a single-clamp design for one operator, the MR 500 produces 600 books per hour. Its Document Verified System ensures that the cover and the inside book match.
Designed for Automation
Rosback Co. offers the model 882 perfect binder, now with PLC touch controls for automated setup. This hot-melt unit provides spine milling and notching at speeds up to 600 cycles per hour. It features up to 2˝ thickness and a self-adjusting nipper. Other capabilities include a precise pulsed temp controller, side gluers and knock-up device for perfect cover registration.
The KM 410.C perfect binder from Kolbus America has a speed of 15,000 cycles per hour. It is equipped with the Copilot system for short makeready times and error-free operation.
The Bourg Binder BB2000 from C.P. Bourg produces perfect bound books with covers, or padded documents. It binds from two sheets to 2.36˝ thick, 1.97x4.3˝ to 17.7x12.6˝. The Bourg BB3001 produces 500 books per hour and is equipped with Bourg Automated Speed Optimization. The BB3001 can automatically adjust carriage speed according to thickness.
Prim Hall remanufactures binders for complete binding systems designed for medium to long runs with speeds up to 18,000 copies her hour.
In the area of pad makers, Brackett offers a circular padder, a hot-melt adhesive padding system that produces pads and pad strips up to 1˝ thick and 19˝ long. It produces at a rate of up to 3,400 units per hour. Other offerings from Brackett include the X-30 system, which automatically pads and tapes in one operation.
Kansa Technology offers the Kansa Series III padding machine for 2x2˝ pads and up to 38x16˝ padded strips. The unit has stainless steel trays and can produce 2,300 padded strips per hour. Features include hot-melt adhesive and temperature that is controlled by a digital-readout controller.

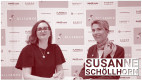



