LUCERNE, SWITZERLAND—Faster web speeds. Wider press platforms. Full color bleeds. Unique product applications. Integrated finishing. The growth and emergence of high-speed, continuous-feed digital printing presses are requiring print-on-demand operations, data centers and direct mail shops to look at the output engine as just one part of the buying equation, given the needs for pre/post paper handling and finishing systems that are compatible with today’s high-speed presses.
That was readily apparent to the nearly 4,000 attendees who converged at the eighth bi-annual Hunkeler InnovationDays, held recently in this quaint Swiss city nestled along Lake Lucerne. With more than 60 companies represented, including major digital press providers Canon, HP, InfoPrint Solutions, Kodak, Océ, Screen, Xeikon and Xerox, the “mini” trade show focused on a broad range of system configurations to showcase a comprehensive, systems approach to continuous document production.
Each day, integrated systems that incorporated equipment from different manufacturers output numerous direct mail, transpromotional, book, short-run newspaper, RFID, continuous form and label applications. By combining the pre/post printing processing of Hunkeler innovations, among others, with finishing offerings from companies such as Horizon, various roll-to-roll and roll-to-sheet jobs were being produced—all at very high speeds, with minimal downtime and requiring limited operator manual intervention.
As the North American distributor for both Hunkeler paper processing and Horizon finishing equipment, Andover, MA-based Standard Finishing Systems hosted a group of leading U.S. printers, direct mailers and in-plant managers to witness InnovationDays 2009. Standard was represented by Steven Reny, president; George Vergilis, director of sales; Bob Flinn, director of business development; and Johan Laurent, Hunkeler business manager.
A sampling of the many technology demonstrations follows:
• The Océ stand featured the world premier of on-demand book production with dynamic format changes (81⁄2x11? to A5) in the folding machine, down to even a single copy. An Océ VarioPrint 6250 cut-sheet printer fed printed book blocks of varying thicknesses and paper stocks into a Hunkeler LS6-S stacking module with integrated signature gluing. This allows secure and simple handling between the production line and the perfect binder. A companion demo showed an SF4 sheet feeder module for nonstop feeding from a paper roll.
• A rollfed direct mail line featured Hunkeler’s new FM6 folder merger module, which combines a plow fold with dual web merging and a longitudinal split cut that can be reset from the folder to the merger function in just minutes. In-line processing was provided by a CS6-II cutting module and a Horizon AF-566F folder. Exhaust of the edge trim and chip-out was performed with the new Hunkeler HKU 2000 system.
• Hunkeler produced a single-sheet, self-mailer on its modular Variweb web finishing system equipped with the new FB 520-W fly-fold belt. Format cutting, tear-off perforation and chip-out functions were performed on the universal module—in one pass—followed by a linear fold on the new plow fold belt. A second demonstration featured the in-line application of an RFID transponder, fold-up smart card and four address labels onto a two-up, folded mailer.
• Kodak announced four new models to its Versamark VL-Series of ink-jet printing systems. Enhancements include optional speeds and resolutions, dye-based inks and MICR support. Also debuting was its new dimensional clear dry ink for the fifth imaging unit of a Kodak Nexpress, which provides a raised or 3D effect.
• An InfoPrint 5000 ink-jet printing system configured for roll-to-fold color transactional printing was equipped with Hunkeler’s FS6 folder-stacker, contact-free PEM520 web cleaning system and WI6-C duplex web inspection and color control system. The WI6-C incorporates fully integrated, dual cameras that monitor the entire web width and automatically signal for the repeat of faulty documents.
• Short-run newspapers were produced on a POPP7 line with a 26.4? web width. Integrated line and spot gluing was provided in the DC7 drum collator. A specially designed Heidelberg Stahlfolder enables large-format variable pagination newspapers (up to 24 sheets).
• HP displayed the easy changeover capabilities between book and transpromo production, including heavy paper stocks, on its rollfed HP Indigo w7200 press.
• Xerox showcased combination lines producing transpromo documents and mailers for either roll-to-roll or roll-to-sheet/stack production on Xerox 1300 monochrome and 490-CF four-color systems.
InnovationDays 2009 also served as the ceremonial passing of the torch from Chairman Franz Hunkeler to his son, Stefan Hunkeler, who become the majority shareholder January 1. According to Hunkeler AG Director of Sales Erich Hodel, the smooth transition will continue the Hunkeler family’s commitment to building the third-generation business. This includes investing more than 10 percent of sales in R&D annually.
“We also place high value in our long-term commitment to the American market and to Standard Finishing,” noted Hodel. “It’s not just a dealer/manufacturer relationship; it’s really a strategic partnership.”
—Mark Michelson



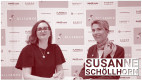

