Top finishing pros reveal their secrets on selecting the right paper cutting tool for the right job.
The cutter is often the last machine to touch the printed product before it goes to the customer, so it needs to cut cleanly, be easy to use and keep the work flowing. Though recent advancements in automation and computer control have made working on the machine easier, they've made choosing a cutter more difficult.
That complexity can be simplified, however, by deciding on three basic factors right from the start: the size, the type of blade, and how many optional features and types of paper handling equipment are needed.
The size of a cutter is dependent on the size of the largest press sheet. All stock should turn easily in the back of the cutter.
Determining Size
"Generally, the rule of thumb is to determine your largest sheet size, measure the diagonal and add a few inches," explains Rob Kuehl, manager of Polar Cutting Systems at Heidelberg USA. To find the diagonal, use this formula: C = square root (a2 + b2).
Rockie Zeigler, president of Original Smith Printing, in Bloomington, IL, agrees that a printer or binder should buy a cutter to accommodate the sheet size of his largest press.
"We have one small cutter among the several we utilize, but all of the rest are sized to accommodate our largest potential press sheet," says Zeigler, who does not recommend buying cutters of different sizes for different functions because that limits the scheduling possibilities.
Nick Adler, vice president of operations at Fort Dearborn Lithograph in Niles, IL, disagrees. "Generally speaking, one size fits all, but that doesn't preclude a mix," he contends, noting that Fort Dearborn runs cutters of different sizes to accommodate different workstations and cutting purposes.
The blade is, of course, the most important component of the cutting process. A blade needs to be durable and provide a clean cut. Today, a printer or binder has three types of blades to choose from: regular hardened steel, high speed steel (HSS) and carbide.
Choice of Blades
"Regular steel should not even be considered," says Kuehl. "HSS knives give you the quality and longer durability needed to meet desired needs, and carbide knives are very expensive and are usually reserved for specialty stock."
Adler agrees that HSS knives are the ones Fort Dearborn uses for most jobs. However, he believes the blade is "such a marginal cost of the cutter that you should buy what you think is the best. We have one of our divisions experimenting with carbide, but I think the jury's still out on it."
Dan Maliniak, vice president of Allied Bindery, in Madison Heights, MI, also sees the advantages of HSS over carbide. "Carbide blades cost twice as much to buy, cost twice as much to sharpen and don't last much longer," he says.
The blades at Fort Dearborn are changed nearly every other day.
Once a decision is made on the type of blade, the next step is how to service it. Blades must always be sharp—a dull blade can result in paper pulls and nicks in the finished product. Thus, there must be a backup supply of blades readily available.
Adler says the blades at Fort Dearborn are changed nearly every other day to keep them at their best. "Servicing the blades is a critical component of the cutting process. If you have to change the blade once a day, then change it once a day," he says, noting that Fort Dearborn keeps multiple sets of blades on hand at all times.
Now that the size of the machine and the type of blade have been decided, a printer or binder is left with the most difficult questions: How much optional equipment is needed? How much can the budget afford?
Optional Equipment
Zeigler recommends buying every option possible, such as Polar's Autotrim. With Autotrim, the cutting table opens up after the cut is made, allowing the waste to fall through and be transported to a bailer or waste removal system.
"Cutters have been very labor-intensive and, when we began buying optional equipment, the increase in efficiency and productivity was significant," Zeigler claims.
Now that the machine and blade have been decided, a printer or binder is left with the most difficult questions: How much optional equipment is needed? How much can the budget afford?
In fact, according to Zeigler, the most important piece of optional equipment he purchased was the Transomat off-loading system. By helping move paper without heavy lifting, he says the Transomat helped Original Smith Printing eliminate many of its workman's compensation claims.
Maliniak shares the same sentiments about his automated Polar System 2. "Our workman's comp guy loved it when he saw it," he exclaims, describing the impact of the system, which consists of a stacklift, jogger, counting scale and off-loader—with the cutter at its heart.
To emphasize the point, Maliniak points out that Allied Bindery has a cutter operator who has been with the company since its beginning; that operator recently turned 65. Maliniak says the operator thought about retiring because of all the heavy lifting and overtime associated with his job, but now he plans to stay around.
According to Maliniak, the addition of the Polar System 2 practically eliminated overtime, retained a strong employee and postponed the search for, and subsequent training of, new personnel.
"With the new system, the cutter operator produces four times as much work, and he's not as tired as he used to be," contends Maliniak. "The expense of the off-loader was paid back in about a year between efficiency and wages."
Adler was equally concerned with efficiency at Fort Dearborn, where millions of labels are printed each year. "The goal was to obtain the ability, once the label was cut, not to touch it again until it was put into the box," Adler says of the off-loading systems. "When you handle something more than once, you have the possibility of mishaps and, in our case, mixes [mixed up labels]. You could be putting a bundle of corn into a box of green beans."
Automating the cutters was part of Fort Dearborn's recent bindery "overhaul." Adler says the company completely redesigned its bindery to automate various tasks, redeploy employees and reduce its workforce by 30 percent. Adler says upgrading the cutters was a large part of that change.
As a final piece of advice for the printer or binder shopping for a cutter with optional equipment, Adler offers this simple piece of advice: "Go out and visit people who use the equipment. Talk to the operators and management about their overall success with it. Learn what the value is and try to run some cost benefits on it."

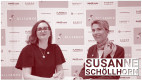



