By Caroline Miller
In the era of earlier job deadlines, shorter runs, increased quality and more complex jobs, efficient postpress operations are imperative to a profitable printing business. All of the efficiencies and savings from state-of-the-art prepress and pressroom capabilities are lost if the finishing department is languishing in neglect.
Upgrading your floor-model folding machine is just one area of the bindery that can offer significant benefits.
By investing in a new folding machine a company benefits from new technology, ensuring much quicker job turnarounds, substantially reduced paper waste, the elimination of the need for high-priced, hard-to-find setup people, as well as a more precise, higher quality, folded product, reveals Stacey Porto, GBR Systems marketing supervisor.
The trends in today's floor-model machines are automation, quality and reliability, says Hartmut Sohn vice president of MBO America.
Today's floor-model folder customers are investing in new folders primarily to reap the benefits of increased automation, agrees Don Dubuque, Standard Horizon product manager at Standard Finishing Systems. "As run lengths decline, setup time becomes a larger percentage of total job time, which drives up the labor cost on jobs. Automation shortens job setup times, which translates into higher profits." He adds that automation also simplifies operation, so more operators can be easily cross-trained.
Less Expertise Needed
Today's new class of automated folders virtually eliminates the need for dedicated and highly skilled "folder specialists" to set up and run the equipment. For example, sheet format and fold patterns can be input on an LCD touchscreen, as opposed to being manually set, then instantly recalled from memory when the job reoccurs.
Finding qualified folder operators to run manual folders can be difficult," Porto contends. "With an automated folder, a typical learning curve can be as little as a single two-day training session. The settings on some folder manufacturers' products are now done via an operator panel that will guide the operator through the setup process."
This automation often replaces most, if not all, of the need for operator makeready and operating skills. "With complex folds, fine adjustments often have to be made, so the benefit of an automated folder where fine adjustments are made one increment at a time at the touch of a button is crucial in a bindery's productivity," she claims.
Quick Setup
The ultimate goal is zero makeready time. Hence today's computer-controlled folder now incorporates automated fold plates, fold roller gaps, alignment rails and delivery rollers. It also has programmable job functions where an operator can store a fold in memory and recall it at the touch of a button. This feature cuts make-ready and fold changeover times significantly, in particular for difficult folds such as gatefolds.
"Fast makeready and quick turnaround times result in high productivity, whilst retaining the highest folding quality available," claims Sohn.
Job memory is a particularly important feature to consider if a user runs a number of different jobs. "This can take labor savings to an even higher level, allowing for instant recall of recurring jobs," states Dubuque.
Versatility is also essential for printers when purchasing a new folding machine, according to Wayne Pagel, president of Kepes Inc. Many processes that were traditionally a separate letterpress operation are now being incorporated into the folding/finishing process. These include high-quality scoring of heavy stocks, pattern perforating, and some cutting and punching operations.
"Printers are being asked to finish a wider range of stocks, in more complex processes," Pagel says. "This calls for modular folding systems that can be reconfigured on a job-to-job basis. The sequence of machinery needed to 'fold' the job may involve 10 or more pieces of folding and finishing equipment. From the feeder on through to the delivery, every piece of the process needs to be able to interchange with another." As a result, he says that few printers can justify a dedicated system only capable of one type of process.
Value-added Functions
GBR Systems' Porto agrees. "Our clients are also looking for a folder with value-added functions, including gluing, nesting prior to folding, pressure sealing, gate folding, soft scoring for toner-based color, and a folder that can operate in-line with cutters, roll unwinds and digital printers.
Finally, while new technology offers new possibilities, there are still some age-old standards to remember when purchasing a new folder.
Quality of construction is still key, especially if you have multiple-shift usage, reports Dubuque. "Check out the drive system, the bearings, the fold plates and rollers. Most of this equipment is purchased on a long-term lease, so customers want to make sure they are going to have an asset that can still perform after 48 or 60 months," he notes.
Last, the quality of the fold is essential, as end-customer expectations have only heightened. As run lengths decrease, fold quality from first sheet to last becomes critical, since there is little or no tolerance for makeready waste or spoilage.
Unfolding What's Available
Floor-model folder vendors offer a wide range of features to fit every need; here is a look at some of the machines currently available in the marketplace.
GBR Systems' Mathias Bäuerle Multimaster CAS 52-B SetMATIC computer-controlled folder is heralded as the first folder with fully automated settings. Fold plates, fold roller gaps (patented design), alignment rails and delivery rollers automatically move into their correct position according to the data entered by the operator on a central control panel. No manual adjustments are necessary, resulting in very short make-ready time, no need for technical setup people, less waste and precise folds.
Circle 401 on Reader Service Card
The Kepes Combi-Unica folder combines the ability to perform multiple plow fold operations with up to five buckle folds in the first unit. It comes prepared for gluing with segmented rollers and fold plates. An extended register table leaves room for tipping operations. The robust construction and 60mm diameter fold rollers permit folding of very thick stocks at high speeds.
Circle 402 on Reader Service Card
The new Standard Horizon AFC-544AKT folder features automated setup through a user-friendly touchscreen. Up to 100 different job settings can be stored in memory, and automated makeready is accomplished in as few as 13 seconds. The feeding section combines a rotary vacuum feeder with a suction head for efficient feeding of a wide range of stock, for sheet sizes up to 21.2x 29.5˝.
Circle 403 on Reader Service Card
The MBO B21 folding machine is available with the standard MS control with automated suction range and sheet gap. Also offered as an option is the MC (micro-processor) control that monitors and controls miss-feeds, jams and sheet length. The top-of-the-line is the Rapidset version that is fully computerized with automatic fold plate adjustments that can be linked to the MBO Datamanager and is CIP-3/4 compliant.
Circle 404 on Reader Service Card
The Baum 15GSL floor-model pile folder is offered with the GSL automatic fold roller tensioning, HDN gear-drive system, toner-release precision urethane rolls, pile air feeder, diagnostic messages, as well as built-in total and batch counting. Handles up to 15x23˝ sheet sizes.
Circle 405 on Reader Service Card
The TD 52, from Heidelberg USA, is designed to handle even the shortest runs. The folder can compress turnaround time between jobs dramatically by automatically positioning side guides and buckle plate positions. A read-out on the operating panel also provides positionings for slitting, scoring and perforating blade, plus fold roller settings. Even a novice operator can follow these easy steps.
Circle 406 on Reader Service Card
The Model 4040 vacuum feed folder, from Profold, features patented "no-set-gap-set" technology, where gap setting is eliminated. Prothane Fast Track Grooved fold rollers provide long life and tight folds. Maximum throughput of 40,000 sph with 81⁄2x11˝, 20-lb. stock. Equipped with stacking tray capacity of 1,000 sheets. Bottom vacuum feeder allows continuous reloading and operation, and eliminates the need for a register table by feeding directly into the first parallel fold section.
Circle 407 on Reader Service Card
The Vijuk H&H KL 112 miniature/pharmaceutical folder offers a quick-set roller adjustment and transfer unit for trouble-free transport. Each station is available with 2, 4, 6, 8, 10 or 12 folding plates for right-angle or tandem configurations. Optional double-sheet detector, bar-code scanner, counter, various gluing systems. It can be equipped with a vertical stacker or shingled delivery system and continuous suction or pile feeders depending on production requirements.
Circle 408 on Reader Service Card
The Signature Feeder/Parallel Folder, from AGE of York, is designed for off-line applications using various feeding mechanisms. It can also be used for in-line applications after trimmers. It accepts loose, glued or stitched products with backbone leading and folds the product parallel to the backbone. The primary use of this system is for producing the additional mail fold of signatures.
Circle 409 on Reader Service Card



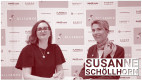

