BY MARK SMITH
Cut, knife, blade, guillotine—the terminology alone explains why safety is a must when it comes to paper cutters. Two-handed cut activation, non-repeat knife cycles and auto-stop infrared light curtains are just some of the safety features that have been mandated by law or become standard due to market demand. Neither the equipment manufacturers nor buyers are willing to compromise much in this area.
While safety still is an important factor in the decision to buy a new cutter, it is an advantage more or less shared by all state-of-the-art models compared to older machines. It is in the area of productivity where the real points of product differentiation can be found, both in terms of the features offered and the capabilities in which buyers are looking to invest. Competitive advantages can be gained from the capabilities of the cutter itself, and/or by building a broader system that may integrate a jogger, stack lift, unloader, bundler, etc.
Programmability and integration of material handling peripherals are not exactly new trends, but they are seeing broader application. Solutions are being offered for a wider range of cutters, and more printers and trade finishers are finding that the ROI adds up.
Running by the Numbers
One particularly active area of product development is in the sophistication of the programming features offered. The base level of computerization—a keypad or touchscreen and visual display—has become the standard, even for smaller cutters. The next step up is the ability to download (from another cutter or computer) job setups via floppy disk or network connection. The current apex of cutter control technology is integration of the CIP4/JDF specification, which some manufacturers have started offering.
The CIP4 (International Cooperation for the Integration of Processes in Prepress, Press and Postpress) organization is working to develop the Job Definition Format (JDF) specification as a way to digitally integrate the entire print production process. The goal is to have job parameters digitally captured once at the front end of the process, then pass that data along the production chain to speed makeready at every stage and eliminate communication errors. Prepress and press operations have been making the biggest push for CIP4/JDF adoption, but its full benefit can only be realized by also tying in postpress.
"Controversial" would be too strong of a word to describe the status of CIP4 integration in finishing operations, but there are differences of opinion about its utility—especially at its current state of development. For obvious reasons, the more market segments (prepress, press and postpress) served by an equipment manufacturer, the greater the incentive and opportunity it has to implement the technology.
Whether it's done digitally or not, there are significant gains to be had from linking postpress operations to upstream processes, asserts Rob Kuehl, marketing director for Polar cutting systems at Heidelberg USA, Kennesaw, GA. Since as much as 70 to 80 percent of the cost of a job already is in the sheet by the time it reaches the bindery, waste becomes very expensive at that point, Kuehl says. The bindery has to find a way to make the materials it's given work, which is typically done by throwing people at the job, he adds.
"CompuCut (and other CIP4/JDF compliant) software can provide a digital link to prepress, but the postpress manager still needs to get involved at the job planning stage to avoid problems in finishing," Kuehl continues. Nonetheless, extending the digital workflow into the postpress arena does provide its own set of advantages, he says. This includes instilling a systematic approach to the work, which results in higher productivity and a better quality.
According to Kuehl, what buyers are looking for in a cutter is safety, reliability, productivity/automation and flexibility—in that order. The safety features of Polar cutters include an electronic light curtain that stops the blade if it is penetrated, a covered backgauge and a 0.5 second time delay in applying the clamp pressure. Along with CompuCut programming, the productivity of the cutters is optimized by a backgauge speed of 30cm/sec., which provides the ability to produce three to four cuts per minute, Kuehl claims.
The company is addressing the flexibility issue by offering material handling solutions, such as its System 6 product, he continues. The system pulls lifts in from the back of the machine and provides a buffer for the lifts so a priority job can be slid in by bypassing the buffer.
Success Isn't Automatic
Among those offering a more reserved assessment of CIP4's potential is Jeff Marr, vice president of sales at Colter & Peterson, Paterson, NJ. "CIP4 is nice in theory, but we are not seeing it put into practice," he reveals. "The standard still needs to be finalized."
While it may be practical for manufacturers that provide prepress, press and postpress solutions to implement the technology, "if you break that loop, it doesn't work," Marr says. He adds that Colter & Peterson has the pieces in place to implement the workflow on its cutters, but it is still waiting for development of the standard and customer demand to reach the point where its implementation is warranted.
Marr says that he has yet to be convinced customer demand will materialize. "You may be able to download the job dimensions, but you still need someone to figure out the sequence of cuts," he explains. "When you add ink and water, heat and pressure to paper it changes sizes. Even if the job specs are communicated properly, you still have to make adjustments at the cutter.
"There also could be operator resistance. I've been in shops where the first- and second-shift operators will cut the same job two different ways. The end result is the same, but the sequence of the steps followed is different," Marr says.
CIP4/JDF still is being refined and isn't an exact standard that manufacturers can generically implement, agrees Bret Stow, marketing director at Perfecta-USA in Indianapolis. Stow says he's starting to see a trend in which buyers want cutters that are CIP4 capable, but the shops are just positioning themselves to implement the technology in the next couple years—not now. Perfecta already has the necessary ports and basic software in place on its cutters, he notes.
Even if job data isn't captured at the prepress stage, shops can benefit from centralization of cutter programming within the finishing department, Stow says. "We are seeing a trend among larger companies with multiple machines to have a 'setup man' (foreman or other cutting expert) program jobs and then use lower-skilled operators to make the cuts. Once a job is programmed, the display will show the operator how the job should be run."
The Challenge Machinery Co. continues to study the benefits of CIP4/JDF, but it isn't actively pursuing implementation of the technology, reports Robb Gould, vice president of marketing/sales for the Grand Haven, MI-based manufacturer. "The market segment we serve has not wanted/needed this feature on our equipment," he explains.
"Challenge's software is very straightforward, which simplifies operator training," Gould continues. "As a result, the printer/finisher no longer needs highly skilled, highly paid operators to complete cutting tasks."
The XT color-display touchscreen programmer for Champion 301⁄2˝ and 37˝ fully hydraulic paper cutters enable job setups to be done on a PC and downloaded to the cutter via floppy disk. By opening the job on the display, the preprogrammed task can be run easily and accurately by the operator, Gould says.
Challenge's top-of-the-line Champion 305 XT cutter features a variable-speed, pinpoint backgauge control and electronic clamp pressure control. It uses hydraulic cutting and clamping action to enable cutting lifts up to its 4˝ clamp opening.
Buyer interest at the recent PRINT 01 exhibition definitely reflected the trend toward systems, reports Perfecta-USA's Stow. "Sixty percent or more of our show leads were not just for a cutter, but a cutter with a jogger or maybe a jogger and a stack lift," he notes. "We saw a lot of interest in the combination of a jogger and stack lift with an integrated weigh scale on our 45˝ and bigger models. Recently we've also had some buyers of 36˝ machines adding stack lifts and joggers."
Perfecta offers cutters in sizes from 30˝ to 66˝, as well as a complete line of material handling peripherals. At PRINT 01, it showed the Cut-O-Drill machine for the first time in the U.S., Stow reports. "It is the only machine capable of cutting and drilling within the same operation."
The manufacturer's cutters feature slotless tables with servo-drive positioning systems to provide accurate backgauge movement. A "Smart Clamp" system is said to sense the pile height and engage the backgauge sooner. Stow says that the machine's control systems employ a flexible touchscreen with color graphics to help guide the operator, and are CIP4 ready.
Since cutting system components typically are modular, shops do have the option of adding pieces as they need them, points out Colter & Peterson's Marr. "The sequence we usually see is a lifting device, followed by a jogger and then an unloader."
Colter & Peterson offers two different lines of cutters, both of which feature U.S.-made computer control systems, Marr says, so the commands are clear and built around how American operators are used to working. The cutters also feature oversized tables that are chrome finished and air cushioned.
The main difference in the higher-end Saber line is its use of a double-end pull of the knife for increased cutting power and greater control over the knife, which boosts performance and cut quality, Marr explains. The product line also offers more features as standard.
Can't Beat the System
One of the motivating factors for the trend toward installing systems is deadline pressures, says Matthew Simons, national finishing manager at MAN Roland in Westmont, IL. (The press manufacturer also markets the Wohlenberg line of cutting systems.) There is a more direct profit motive, as well, he says.
"There is no money being made unless the knife is cycling," Simons notes. "Material handling consumes the largest amount of time in the cutting process. Therefore, automating the way material flows to and from the cutter is the best way to increase production."
At PRINT 01, MAN Roland featured a 54˝ Wohlenberg paper cutter with an integrated waste evacuation system. "By adding a pile hoist, jogger with an air removal system, curved gripper transport system and an unloader to this cutter, we were able to show an increase in production of two to three times that of a standalone cutter," Simons says.
The company also showed the new BA3 unloader, which has a left side-aligning gauge that follows the material during the movement of the table to facilitate handling of very small pieces. In addition, Wohlenberg has redesigned its Cut-Tec 92 product to offer half-size printers the same programming capabilities—including CIP3 interface—available on its larger machines.
There is another facet to productivity, asserts Terry Lee, vice president of sales and marketing at Dexter-Lawson Mfg. in Cambridge, ON. That is the ability to handle a wider range of substrates.
Dexter-Lawson cutters are known for being reliable, heavy-duty cutters, Lee points out. "Our industry-leading 7˝ clamp opening and 63⁄4˝ maximum lift height allow for greater capacity and production output per hour of operation," he says. The machines have the power to cut pieces of material up to 3˝ thick and can handle a range of materials beyond paper, including photographic film, metal plates and cardboard.
The manufacturer's 47˝ to 70˝ cutters offer the same basic feature set, with the exception of dual-drive knife action being standard on the 60˝ and 70˝ models. These synchronized drives, one for each pull bar, are said to pull the knife easily and smoothly through the heaviest lifts. A flex clamp option is also offered on the larger models.
The maximum stack height issue is a littler more complicated, asserts John Porter, division manager at LDR International in Portland, OR. If a printer/bindery is using older equipment, often times it is worn to the point that it can't cut maximum-height lifts of paper accurately, he says. "But, the cycle time of the machine for a 6˝ lift is the same as for a 2˝ lift. Therefore, the easiest way to increase productivity is to maximize the size of the lift being cut," Porter explains.
A unique feature of LDR's Itoh cutters is the ability to program the clamp dwell time. The clamp can be set to stay down for up to 10 seconds after the cutting cycle, so the material can be jogged up against it without the operator having to keep the foot pedal pressed down. The cutters also feature a chrome bed, central lubrication and access to all knife adjustments from the front of the machine to save time and facilitate maintenance. Itoh cutters are equipped with Windows-based software so, if and when customers want to utilize CIP4, the manufacturer will be able to upgrade the software, Porter says.
In a broader context, the quality of cutting can greatly impact the productivity of the overall production process, asserts Mark Pellman, marketing manager at Baum in Sydney, OH. A programmable cutter using HSS (high speed steel) knives can provide more consistent results throughout the run, which facilitates later finishing steps, he explains.
In addition, the ability to easily recall setups and follow on-screen directions help to produce more consistent results regardless of the skill levels of different operators.
Adjustable clamp and knife cycle times to facilitate special cutting needs are a key standard feature on Baum cutters, according to Pellman. The BaumCut 26.4 and 31.5 programmable cutters are fully hydraulic and are available with optional air or non-air side tables. The manufacturer provides infrared light beams and two-hand non repeat cut buttons as standard equipment on all of its paper cutters.
Variations on a Theme
Since MBM Corp. targets the small commercial and in-plant printing markets, its largest cutter is a 251⁄2˝ model, notes Bill Golde, president of the North Charleston, SC-based manufacturer. Add-ons like material handling peripherals and CIP4 support primarily are for the bigger cutters, he says, but similar types of enhancements are being implemented at this level.
"We do offer programmable machines," Golde says. "Our Triumph 6550-EP, for example, has a 10-button electronic keypad and digital readout to preset measurements for the backgauge. There's also a memory key for repeat cuts."
When it comes to safety, putting infrared beam systems on smaller, lower cost cutters isn't a realistic option, Golde contends, but he believes some type of guard still should be standard. "The 6550 has a plastic shield that comes down over the knife, and the cutting cycle can't be activated unless it is in place." The machine also has safety guards on its front and rear tables.
Standard Finishing's 24˝ Horizon APC-M61 paper cutter is said to feature advanced programming capabilities that are easy to use. A highly polished, chrome-plated worktable provides a smooth surface for lift travel and virtually eliminates marking. Dual-speed induction-hardened backgauge screw and forged linear raceway deliver sustained cutting accuracy, according to the Andover, MA-based manufacturer.
For smaller jobs, Standard offers the Horizon PC-45 and PC-64II semi-automatic cutters. The PC-45 offers a 17.7˝ wide cutting capacity, illuminated cut line and a maximum lift of 2.7˝. The PC-64II knife features a precision-built backgauge lead-screw that enables trim cuts as fine as 0.019˝.
Cutronix Technologies recently introduced its new line of Five-star computerized paper cutters in sizes from 30˝ to 52˝. The machines feature infrared safety beams, full air tables, an overhead leadscrew with cylindrical guide and center-actuated clamping. The larger models have a double-pull arm for durability and accuracy in heavier cutting applications. The Markham, ON-based company says that knife changes are fast and simple via a crank-down elevator system, with the knife holder specifically designed to protect the operator.
Given these trends in product development, computerized, systematized, connected and automated may be the more important terms in defining the future of cutters.
Frozen Stiff
High-tech features are nice, but paper cutter performance really balances on the edge of the knife. The longer it stays sharp, the better.
Heat treating and carbide applications have become common practices for increasing knife durability. But now, Cryocore, in Wallingford, PA, is among the pioneering companies hoping the industry will warm up to the concept of cryogenic treatment. The process of slowly lowering the temperature of metal to -320°F in a computer-controlled cryogenic chamber realigns the material's molecules into a more orderly orientation, explains Bill Foth, operations manager. "This greatly extends the usable life of any metal item that rolls, impacts, cuts or slices," he adds.
The technology grew out of the space program, Foth says. NASA engineers noticed changes in the molecular structure of materials exposed to the extreme cold of space.
The improvement in wear resistance depends on the original quality of the knife and type of paper being cut, but edges of processed knives should withstand 60 to 125 percent more cuts, Foth claims. The treatment should only need to be applied once, since a sharpened knife will exhibit the same performance enhancement—if the blade isn't excessively ground until the point where it turns blue, he says. "Cryogenic processing actually makes it a little easier to true up the blade, since about 10 percent less material needs to come off the edge to make it sharp again."
Knives up to 60˝ can be treated at a cost of up to $120 for the maximum length. Customers can expect to have their treated items back within a week of receipt at the processing center.
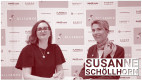




