KBA’s Investment in Manufacturing Operation Is in Parallel to Realignment
Koenig & Bauer’s main facility in Würzburg, Germany: Following substantial investment in new buildings (logistics center, design center, production hall, foundry) after the millennium, in recent months new machining centers for large parts were put into operation.
WÜRZBURG, Germany—June 15, 2015—The consumption of printed newspapers, magazines, catalogs and books, has not been left unscathed by the advance of the internet into more and more aspects of our lives. Print media is forced to share readers and pieces of the advertising pie with a growing number of online channels. In addition, publishing houses are on the hunt for sustainable business models and are therefore often reluctant to invest in print.
Adjusting to a smaller market
This affects press manufacturers in media and advertising-orientated markets. The global market for sheetfed offset presses has halved since 2007, and demand for web offset presses for larger runs has shrunk by over three quarters. Over 15,000 jobs have been lost alone at the three biggest German manufacturers Heidelberger Druck, Koenig & Bauer (KBA) and manroland given the necessary adjustments to capacity.
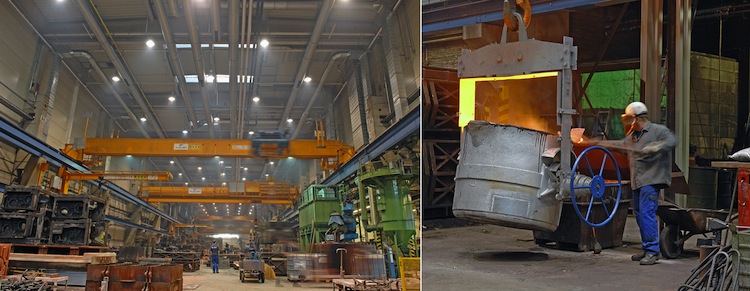
Complex large parts weighing up to 12t can be cast by hand in the foundry (KBA-Gießerei) which was refurbished for over €14m in 2011.
Fit@All program on the home straight
KBA has now largely implemented its Fit@All program for the realignment of the company in place since the beginning of 2014. The extensive package of measures includes the relocation of over 50 machine tools preventing parallel activities at the production sites. The plants in Ternitz and Trennfeld have been closed and sold. The cut of a total of 1,500 jobs announced in 2013 is virtually complete. Furthermore, on May 21, 2015 the majority of the KBA AGM approved the company realignment under company law proposed by the management board. This stipulates the conversion of the parent company, Koenig & Bauer AG, into a management holding following the spin-off of four operating subsidiaries for the business units digital and web (KBA-Digital & Web Solutions), sheetfed (KBA-Sheetfed Solutions), security printing (KBA-NotaSys) and production (KBA-Industrial Solutions). The four spun-off companies will have a German legal status of an AG & Co. KG (limited partnership) with the parent Koenig & Bauer AG as sole general partner. The holding company’s management board, which primarily will take over strategic and central tasks, is to be reduced to three members.
Large parts up to 5m long and 3m wide can be scanned for their accuracy in micrometer in an air-conditioned measuring room. Deviations equal to the thickness of a single hair are too big.
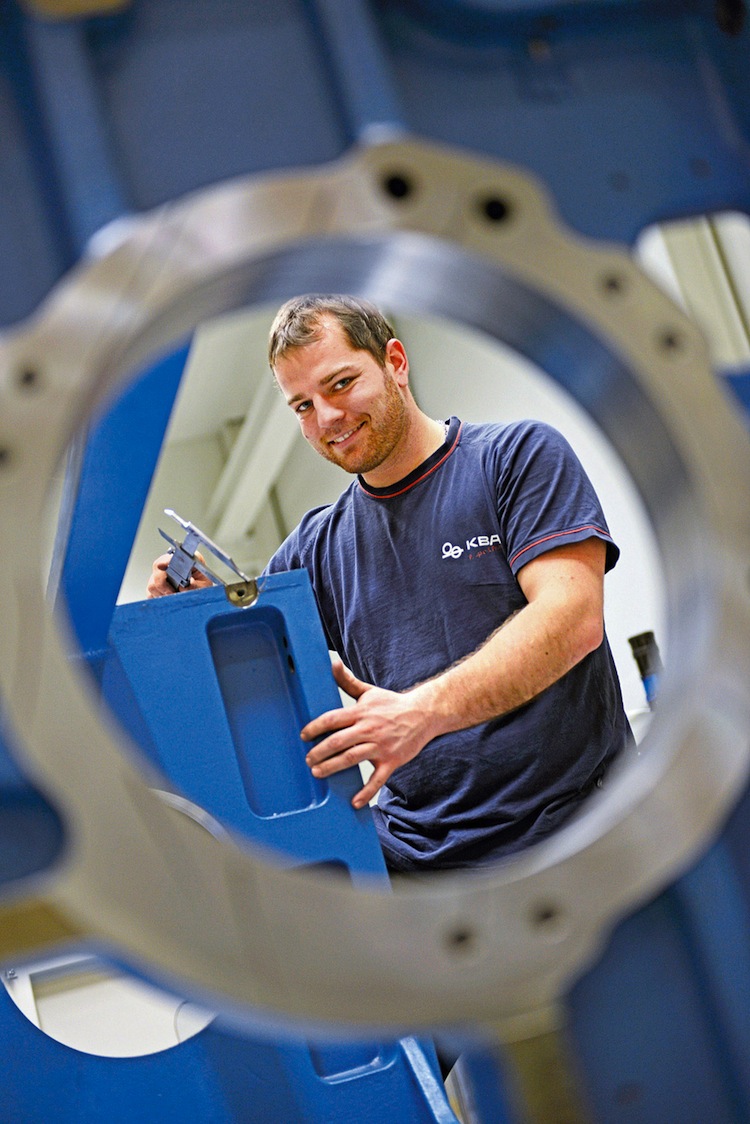
Approx. 1,300 employees, including 540 skilled workers and 113 apprentices, currently work at Koenig & Bauer’s main site compared to over 2,000 in 2007. KBA was forced to realign itself due to the slump in demand for web press lines for publication and newspaper printing.
After the entry of the new companies in the commercial register at the beginning of July, this new structure will be implemented from Jan. 1, 2015, retrospectively. The management board expects the new structure to deliver more transparency in terms of costs and earnings, as well as improved profitability through internal customer supply relationships.
(From left) Member of parliament Oliver Jörg and KBA CEO and president Claus Bolza-Schünemann at the KBA RotaJET digital press.
New markets in focus
Excluding apprentices, trainees and employees on phased retirement schemes, at the end of March 2015 there were 4,711 employees on group payroll. This was over 3,000 less than eight years ago. In 2007 group sales still stood at €1.7bn compared to €1.1bn in 2014. KBA’s previously core web offset press business has shrunk the most. Along with its main site in Würzburg, the factory in Trennfeld and the plant in Frankenthal/Palatinate were especially affected by this market slump. The missing sales volume could only partly be replaced with business opportunities in digital and packaging printing.
KBA is therefore actively pushing forward with the expansion of its product portfolio and strengthening its market position in growth areas. In addition to its own new product developments, this strategy includes company takeovers, such as KBA-Flexotecnica and KBA-Kammann in 2013, and partnerships with other firms. For example, an inkjet press for corrugated packaging to be unveiled at the Würzburg site in November co-developed with American manufacturer Hewlett Packard (HP).
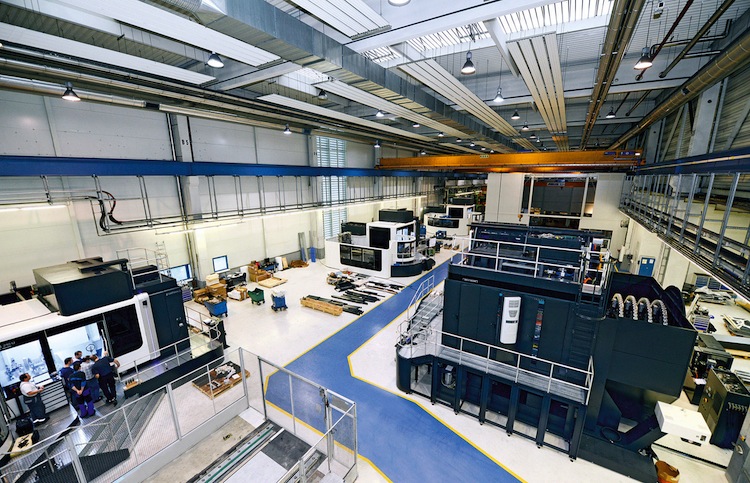
Highly productive machining centers are the heart of large part manufacturing in hall 1 at the KBA site in Würzburg.
Print in all its diversity has a future
The repercussions of the structural shift in the print and media arena are well publicized. At times the impression is given that print is only heading downhill, but this is not true. Stable and growing markets for printed matter exist, e.g. packaging and new industrial applications. The world’s oldest and second-largest press manufacturer continues to believe in print and a positive future for its main site in Würzburg despite necessary cutbacks in recent years. This is why the company invested €14m in 2011 in renovating its foundry and recently more than €7m in production facilities in Würzburg with the installation of five high-tech machining centers, as KBA CEO and president Claus Bolza-Schünemann reported during a tour of the site.
(From left) On the first production open day, Executive Vice President for Production Michael Kummert, and KBA CEO and president Claus Bolza-Schünemann, welcomed deputy mayor of Würzburg Adolf Bauer, technical college president Prof. Robert Grebner, and numerous other representatives from government offices and the industry to the KBA main site in Würzburg.
KBA-Industrial Solutions also for others
Along with side frames, ink ducts, round drums and other components for KBA presses, the new business unit KBA-Industrial Solutions aims to cast and precision machine challenging large parts for external mechanical engineering and plant manufacturers. This has already taken place successfully for a raft of renowned companies. As well as producing various components made of casting, steel or metal, KBA-Industrial Solutions is also able to offer assembly, engineering and logistic services. It is thus an interesting partner for other machine manufacturers looking to outsource or in the event of capacity shortages. Accordingly, in addition to Würzburg KBA has also invested strongly in its plant in Radebeul, Saxony, including the latest coating units.
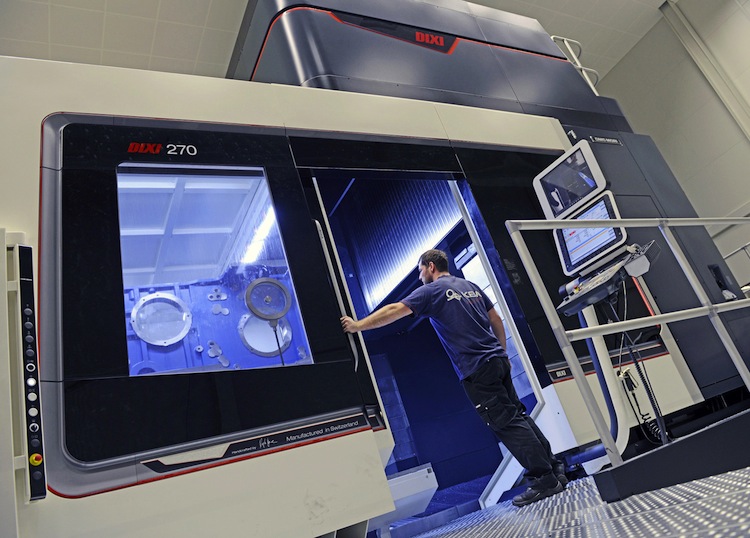
A high-tech DMC 270 (DIXI) milling machine processes large parts with painstaking precision in an air-conditioned room.
Commitment to traditional site in Würzburg
Compared to other German machinery engineers, the cutting-edge production facilities at both KBA main plants are anything but the norm. Claus Bolza-Schünemann and his colleague Michael Kummert responsible for production view this as a commitment to the company’s traditional main site in Würzburg and proudly gave representatives from politics, business and government institutions as well as external manufacturing clients and journalists on a tour of the site on the first production open day on June 12. Teachers and students from the region were also invited to the cradle of press engineering in order to find out more about the various training opportunities offered by the company and the KBA state-recognized in-house training school. With a training rate of 7 percent of the workforce Koenig & Bauer has an outstanding reputation when it comes to educating the next generation of young skilled staff.
Along with side frames and other components for presses, KBA-Industrial Solutions casts and processes challenging large parts for external machinery and plant manufacturers.
In addition, on June 13, current and former KBA employees plus their families are invited to see what has changed as part of the realignment in the production and assembly halls on a second production open day as many do not see these activities on a regular basis.
An open day for the general public, like the one in September 1992 which attracted several thousand visitors, is planned for September 2017, in celebration of the company’s 200th jubilee.
- Companies:
- KBA North America