Push Solutions Adds RMGT 9 Series with LED-UV to Meet Retail, Packaging Needs
NEW BERLIN, Wis. — March 21, 2016 — Why would a printing firm competing in the highly competitive retail marketing, retail packaging and nationwide field distribution segment of the print market make the leap into the full-sheet arena in just four short years? The answer is that having quadrupled sales since their foundation in 2012, partners Brad Flagge and Nick Bova saw no reason to slow down simply because they had reached capacity in their manufacturing plant. The investment in a new RMGT 9 Series press more than triples their capacity so the meteoric trajectory of well-named Push Solutions can push on into the future.
Despite growing their staff from nine employees to 24 and running their existing Heidelberg equipment around the clock, Push Solutions highly demanding clients still needed more and more volume and shorter and shorter delivery times. “Serving our local customers throughout the Southeastern Wisconsin market and also our high volume retail customers in New York and Chicago was becoming a huge challenge,” states Nick Bova, VP. “Our projects are seldom a single process order so post print finishing, kitting and special field distribution adds time to our projects. We had to compress our timeline to continue our rapid growth plans. The LED-UV curing and full-sheet production of our new RMGT press has changed our entire approach to production. In addition, we are very excited about our future opportunities producing high value products for our customers. Printing on synthetics, plastics, vinyl and foil materials will really leverage the power of our LED-UV technology and our new RMGT press.”
Push Solutions need to expand capacity was really accelerated by their retail marketing and retail packaging clients, so the next decision was what brand of offset press to invest in to meet their customers’ demand. “The highest print quality, reliability and responsiveness from our equipment provider were our primary concerns,” comments Brad Flagge, president. “When Nick and I looked at the new RMGT 9 Series at Graph Expo 2014, we were very impressed. The vibrant color and instant curing of the sheets with LED-UV and the extremely fast make-ready was a great fit for our production needs. Every RMGT customer we spoke to raved about their experience, from installation to press productivity, so we decided to move forward and buy the 9 Series.”
Since commissioning their new RMGT 920ST-5+CC+LED-UV+IR in late January, the staff at Push Solutions has not only completed Graphco’s in-depth training regime and achieved G7 color standardization status, but also insourced dozens of jobs that were previously jobbed out. “Working with the Push Solutions pressroom staff was a real pleasure,” says John Arnold, technical service manager for Graphco, the RMGT Distributor for the Midwest. “It’s great to work through our training process with such professional pressmen.” Joining the new RMGT 9 Series is a new full size CTP system, so the G7 process was smooth and efficient.
The press configuration chosen by Push Solutions includes a full array of RMGT Smart technology including the patented Smart Insta.Color makeready technology, 16,000sph production speeds and RMGT/Panasonic LED-UV Curing along with IR/Hot Air drying to provide Aqueous Coating when that is appropriate for their customers’ needs. Brad Flagge adds, “Speed to market is key for our retail marketing and packaging customers and nothing beats LED-UV when it comes to moving our customers’ projects through the plant. The efficiency we have already achieved is proving out our theory that the RMGT 9 Series is the lowest cost-to-print on the market and our finishing house loves our powder-free and completely dry printing. Our pressmen have commented on the workplace and environmental advantages, as well since the new press is so much easier to run than our old press and with no VOCs or powder the pressroom stays clean and odor free." Flagge says RMGT was the only press manufacturer to satisfy all five of their requirements for power consumption, footprint, color control, automation and cost.
“We are proud to be part of Brad and Nick’s success and it’s certainly exciting to work with such a fast growing and results-oriented organization. Based on how quickly their team has adopted the new RMGT technology, we feel a great partnership has emerged between Push Solutions, RMGT and Graphco,” states Derek Gordon, Midwest regional manager for Graphco.
About RYOBI MHI Graphic Technology
RYOBI MHI Graphic Technology (RMGT) is among the world’s largest manufacturers of sheetfed offset printing presses and the world leader in LED-UV technology with over 165 placements worldwide. Its high-speed, fully-automated presses are respected worldwide for unsurpassed print quality, low total cost of ownership, extreme ease of operation, and unmatched reliability. In partnership with Panasonic, RMGT released LED-UV Curing for Print at Drupa 2008 and it now offers the only G3 LED-UV technology on the market. Headquartered outside of Hiroshima Japan, RMGT is a joint venture company bringing together the best technology and manufacturing expertise of Ryobi Limited and Mitsubishi Heavy Industries. The enhanced product lineup and strengthened manufacturing prowess makes RMGT an indispensable brand for the printing industry.
About Graphco
Graphco is the industry’s leading provider of offset, digital, and print finishing solutions. Along with other GSNA members, we proudly import the RMGT line of new offset printing presses featuring LED-UV curing technology, Smart Insta.Color automated makeready, and our popular Packaging Edition presses. All RMGT presses offer best-in-class reliability and durability. The Graphco Technical Service Team stands behind every RMGT press and Graphco offers top-notch service. Since 1976, Graphco has thrived in an ever-changing market place by loyally adhering to its original model for success: Providing best-in-class print production equipment along with reliable and assured technical service.
Source: RMGT/Graphco.
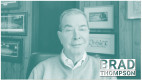




