For a long time, offset lithographic pressrooms have been reaping the benefits of curing inks and coatings with ultraviolet (UV) radiation instead of drying them with spray powder and/or heat.
The end result: a fully set, ready-to-finish sheet, is the same with both methods. But, instant UV curing sends the sheet to the bindery much faster than waiting for it to dry in a stack on a pallet — a major gain in productivity over standard drying, and only one of the advantages that UV technology brings to printing.
Conventional UV lamps emit UV radiation by passing electricity through mercury vapor and other chemical compounds inside a tubular glass bulb. It’s a proven technology, but during the past 10 years, UV systems developers have learned how to accomplish the same thing with mercury-free light emitting diodes (LEDs) as the UV source.
The newer process, LED-UV, isn’t intended to be a wholesale replacement for its well-established predecessor. However, it has a number of distinct technical advantages over lamp-based UV, and these, manufacturers and other experts agree, could make it the UV solution of choice for many printing and packaging applications.
Bill Bonallo, president and CEO of IST America, sees LED-UV catching on in the long-perfector segment, as well as among “general conventional, oil-based commercial printers” with limited or no previous UV experience. He says “the oil-based guys are most captivated” by the prospect of getting fully dry sheets to work with, having cured them either with in-line LED-UV units or a combination of LED-UV units and conventional lamps.
Rapid Pace of Sheetfed Press Retrofits
Retrofitting sheetfed presses with LED-UV curing systems remains the “fastest moving” market opportunity for the technology, according to Hans Ulland, VP of sales – Americas, at AMS Spectral UV (formerly Air Motion Systems).
In addition, he says, “web offset is coming up incredibly fast,” as these printers realize that they can have LED-UV units in lieu of hot-air ovens on this type of equipment. Ulland reckons that in packaging, four out of five of his company’s UV sales in Europe and North America are for LED-UV, which he also identifies as the “standard” UV method on the commercial side.
Jeffrey Woloshyn, sales director of Eltosch Grafix America, similarly notes that his company’s UV quotations “are highly skewed to LED” and are likely to stay that way. Commercial and packaging are the main applications and, in the latter, he says, “the only thing they’re not doing is food” because of regulatory restrictions on UV inks for food packaging.
The appeal of LED-UV lies in its high efficiency. Jennifer Heathcote, founder of the Eminence UV consultancy and secretary of RadTech — a trade group for UV and EB (electron beam) curing technologies — cites instant drying, minimal heat transfer to substrates, elimination of ozone and solvents, and long diode life as LED-UV’s principal advantages.
There’s also the fact that unlike conventional UV lamps, LED-UV units switch on instantly without a delay for a ramp-up to full power. “They don’t care” how many on/off cycles they’re put through, says Heathcote, since it doesn’t affect performance.
Watch the ‘Clock’
Bonallo points out another efficiency-boosting, energy-saving difference between the two methods: the ability to “clock” LED-UV exposure so that it is formatted strictly to the area to be printed, instead of illuminating the entire sheet as a conventional lamp does. The low-heat operation of LED-UV units makes them suitable for “hyper-temperature-sensitive substrates” like plastic, he adds.
Woloshyn’s litany of praise for LED-UV curing includes the low cost of maintaining the exposure units, in which diode life can be as long as 20,000 hours. Ease of operation is another powerful selling point. Press crews, he claims, are the biggest advocates of LED-UV because of the way it simplifies their production routines.
Don’t forget, advises Ulland, that retrofitting a press for UV curing can be done with fewer LED-UV units than conventional lamps. A single LED-UV source, he says, matches the curing capacity of multiple mercury lamps at a fraction of the energy consumption.
Ulland notes that besides saving costs, the technology is kinder to “human values” with its low-temperature, odor-free operation. This makes printers “much more accepting” of LED-UV than they are of the heat and the smell sometimes associated with conventional UV systems.
Consultant Allen Jenkins, who is also executive director of the International LED UV Association, points out that the people in the pressroom aren’t the technology’s only beneficiaries.
Designers, he says, “love the feel of uncoated stock, but they don’t want the images to look like they’re on an uncoated stock.” By minimizing ink absorption into uncoated papers with its instant cure, LED-UV gives designers the color pop they want without obliging them to print on coated grades.
Bean Counters’ Bonanza
But, it’s not just about good-looking sheets — with LED-UV, production economy and stability enter the picture as well.
According to Jenkins, “My customers who are real bean counters love it,” when they calculate the time and money they’ve saved by avoiding spray-powder cleanouts and other issues associated with non-UV drying. The process is so production-friendly, he says, that he has even seen digital presses at work in the same pressrooms as LED-UV equipment.
Despite its many attractions and increasing adoption, however, LED-UV curing isn’t likely to become a disruptive technology that pushes conventional UV curing to the margins. The original process, Bonallo declares, “is rock-solid, and isn’t slowing down:” evidence of which can be seen in the fact that most of IST America’s UV placements this year have been conventional systems.
As in all other forms of printing, the application dictates the choice of technology. This explains why conventional UV’s bulwark continues to be packaging, where the process gets to play to all of its recognized strengths.
Bonallo says “packaging and high-end packaging are staying firmly with traditional UV” because packaging printers want to avoid the “risk factor” inherent in switching to LED-UV inks and coatings, which are formulated differently. Packagers, according to Bonallo, “are not experimentation guys. They know what works.”
Jenkins, likewise, calls this the reason for what he describes as a “resurgence” of conventional UV installations by packaging printers in 2019.
Are Brands Change-Averse?
Brand owners tend to be conservative as well. Heathcote observes that if the bulk of what a printer produces is for brands, changing from conventional to LED-UV curing might involve requalifying color matches under the new process. That could be challenging for cosmetics, spirits, and other categories with tight color specifications, she points out.

An LEDcure SCR unit from IST is mounted in a frame to simulate the installation on a narrow-width web press.
Coating is another consideration. Ulland advises printers who coat “virtually everything” that they may get a better ROI by sticking with conventional UV, which offers them a broader range of less expensive coatings than LED-UV currently does. He says, nevertheless, that AMS Spectral UV is seeing considerable movement toward the newer process by packaging printers that are prolific coaters.
Printers ready to embrace LED-UV curing can choose from among three ways to do it: by buying a new offset press with factory-installed units; by retrofitting an existing, non-UV press with them; or by replacing conventional lamps on an existing press with LED-UV modules.
The choice will be case-by-case. Ulland says that built-in and added-on LED-UV units “operate identically” and that the cost of retrofitting for LED-UV will be less than that for conventional UV because there will be fewer sources to install.
Bonallo agrees that the performance of original and retrofit LED-UV systems should be equal “in theory.” But, he notes that every integration is unique and that variations — for instance, in the positioning of the UV emission source and the amount of space between it and the substrate — can yield different results.
It’s Still Legacy Iron
Something else to bear in mind, counsels Jenkins, is that retrofitting LED-UV onto a legacy press won’t do anything to increase its running speed or shorten its makereadies. The curing will be there, but without the productivity-enhancing automation features that a new, LED-UV-equipped press would bring.
As for replacing conventional lamps with LED-UV sources, Bonallo says it can be done with the help of an electronic power system from IST America that supports both processes. This, he claims, provides a “no-risk, future-proof UV solution” for customers who then can “hot swap” one set of modules for another.
But, Bonallo also notes that retrofitting and replacement grow harder to justify as new presses with integrated LED-UV become increasingly productive from end to end. The question, he says, is whether the cost of the add-on will be worth achieving “a little bit more throughput” on a legacy press that, except for the curing, isn’t competitive with newer models.
Another question touching the adoption of the technology concerns the availability and cost of LED-UV-compatible inks and coatings. When the first LED-UV systems began to appear, choices were limited, and the price spread between LED-UV and conventional UV consumables was large. Since then, there has been some improvement on both counts.
Supply and Prices of Inks and Coatings
In terms of supply, says Heathcote, “the inks are there,” and coatings are “getting better” as the consumables manufacturers bring more formulations to market. She thinks that although LED-UV ink pricing continues to be “a little bit more expensive” than conventional, it is trending in the right direction thanks to growth in demand. Heathcote acknowledges, however, that the higher ink price could be hard to support in low-margin production environments.
“Essentially equivalent” is Ulland’s assessment of ink pricing. “Pretty close” is Woloshyn’s, with both agreeing that coating prices remain higher on the LED-UV side. The price gap in coating “is still a big, big, difference,” according to Bonallo, who cites tariffs on raw materials imported from China as one reason for the disparity.
None of this appears to represent an obstacle to the continued growth of LED-UV curing for offset presswork. Particularly optimistic is Ulland, who reports that 75% of AMS Spectral UV’s current sales volume in North America consists of LED-UV systems and equipment. He says strong interest in the technology is also coming from non-print-based, industrial customers such as makers of automotive products and OLED television sets.
This is happening in part, according to Ulland, because LED- UV “is an easier-to-capitalize way to add radiation curing than conventional UV.” As a result, he foresees having “an endless supply of printers who want to convert” to the technology.
Keeping Perspective
Printers moving in this direction should heed Heathcote’s advice that an LED-UV curing system, however potentially valuable it may be, is ultimately just “a piece of kit” that won’t solve 100% of their production challenges. Each system, moreover, is different, leading to mismatches between LED-UV units and presses that aren’t correctly paired.
“With all new technology, it’s difficult to understand what’s important,” she says, urging printers to make sure that all elements of their intended LED-UV production workflows, including applications, are compatible with one another.
For making this happen, there may be no better guidance than the wisdom that comes straight from the pressroom floor.
Jenkins says that when he speaks with owners about implementing LED-UV, “I always tell them, get your operators involved in the due diligence.” Companies that “shelter” their press personnel from technical advancements have a harder time adopting them than companies that can draw upon the knowledge of a well-informed production team, he explains.

Patrick Henry is the director of Liberty or Death Communications. He is also a former Senior Editor at NAPCO Media and long time industry veteran.
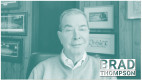




