With LED-UV for Sheetfed Offset, the ‘Wait’ Is Over
As Bill Bonallo, president and CEO of IST America, correctly observes, “nowadays, nobody wants to wait for a sheet to dry off press.” But, before the advent of UV (ultraviolet) curing as an alternative method of drying, that’s what sheetfed offset printers typically had to do, even with the aid of offset spray powder and other traditional ink-setting techniques.
The drying step began to grow less time-intensive with the introduction of on- and off-press UV curing systems in the 1960s, and that original technology still predominates among the energy-curing processes used by the printing industry. Roughly 10 years ago, curing by means of light-emitting diodes (LEDs) as an alternative to mercury vapor lamps entered the market, giving printers more options for eliminating the drying bottleneck from their pressrooms.
Although LED-UV has certain advantages over conventional UV, it’s best understood as an adjunct to, not a replacement for, the older process. That said, LED-UV has made remarkable technical gains in the relatively brief time it has been available. Printers — especially those with older presses in need of a quick-dry retrofit — are finding it a flexible and cost-efficient way both to increase job throughput and enhance the quality of the finished product.
The rising interest accounts for the fact that up to 70% of the curing systems supplied by AMS Spectral UV for print and non-print applications include LED-UV components, according to Hans Ulland, the company’s VP of sales for the Americas.
Demand is strong in the sheetfed offset segment, where 65% of the business in UV curing comes from LED-UV. Even packaging, which had been “last on board” with LED-UV because of that market’s general safety concerns about UV curing, is now embracing it, Ulland says.
Long List of Benefits
Jeff Woloshyn, sales director at eltosch grafix Americas, similarly reports that up to 60% of the company’s current sales volume in UV consists of LED-UV systems and equipment. Among the technology’s attractions for sheetfed printers, he points out, are its low energy consumption compared with conventional lamps; the long life and easy maintenance of its diode arrays, which come immediately to full power without warmup; its mercury- ozone-, and VOC-free operation; and the gentleness of its low-temperature exposure on heat-sensitive substrates.

AMS Spectral UV does about 65% of its business in UV curing for the sheetfed offset segment with LED-UV modules like the one shown above.
All of this is possible because LED-UV, like conventional UV, doesn’t dry inks and coatings through heat and evaporation the way traditional sheetfed offset drying systems for oil-based inks do. Instead, it cures them by exposing the energy-activated photoinitiators they contain to UV radiation, causing the fluids to polymerize. This hardens them almost instantly, forming a dry, durable layer on the surface of the sheet.
Because polymerization takes place within one range of spectral wavelengths for conventional UV lamps, and within another, narrower one for LED-UV arrays, inks and coatings have to be formulated separately for each type of exposure. The wavelength difference also accounts for the fact that while conventional, mercury-based lamps can cure LED-UV-compatible inks and coatings, LED-UV arrays can’t do the same for conventional UV fluids.
However, this doesn’t preclude using both processes on the same press — a best-of-both-worlds combination that saves printers money.
Bonallo points out that because LED-UV coatings are still significantly more expensive than their conventional UV equivalents, “the vast majority of printers utilizing LED-UV in between or after the print units still run traditional UV in the press delivery to cure traditional UV coatings over LED inks.” The additional hit of energy from the end-of-press mercury lamps may provide some extra curing “insurance” for the LED-UV inks, he adds.
Configuring a new press, or retrofitting an existing one for LED-UV curing, is relatively simple: one LED-UV array does the work of multiple lamps on a press running conventional UV, and the LED-UV unit can be flexibly positioned to suit the type of curing needed.
Ulland describes, for example, how one of his customers replaced four interdeck UV units on a legacy press with one LED-UV array between the last printing station and the coater, keeping a single UV unit at the delivery. The removed UV units furnish spare parts for the remaining one.
“We sell efficiency,” Ulland says. “You should almost never need more than one LED-UV unit unless you’re doing something special.”
Perfecting Perfected
Quick curing with LED-UV is also a welcome remedy for sheet marking in perfecting sheetfed printing, where both sides of the sheet are printed in one pass. Alan Jenkins, an LED-UV print consultant, notes that marking occurs when wet ink on the side printed first contacts transfer cylinders after the sheet is turned over by the perfecting device. Subsequent sheets pick up the unwanted ink from the cylinders, causing marking, which Jenkins identifies as the main headache for sheetfed perfecting.
The most common way to counteract marking was to wrap transfer cylinders in nets of ink-repelling material. A different solution, according to Bonallo, is to install LED-UV arrays after the first set of printing stations, just ahead of the perfector, and after the last printing unit before the delivery. That way, he notes, sheets are dry before the flip, and the risk of marking is minimized.
The appeal of benefits like these explains why increasing numbers of new sheetfed presses are being delivered with LED-UV curing built-in. Other print market segments have already seen the light. For example, most narrow-web flexographic presses for labels ship with LED-UV modules that enable fully dry printed rolls to go straight to converting and finishing.
A 2018 study by the PRIMIR research unit of the Association for Print Technologies, based on data supplied by I.T. Strategies, forecasted that by 2021, more than 25% of new sheetfed offset presses would be sold standard with LED-UV curing technology. The opportunity for perfectors was said to be even stronger, with LED-UV curing’s share of new perfecting sheetfed offset press sales expected to reach nearly 40% by 2021.
But the biggest market for LED-UV probably lies in retrofitting it onto conventional, non-curing sheetfed offset presses. According to the PRIMIR study, 90% of LED-UV sales for straight (one side) presses, and 80% of sales for perfectors through 2021 would consist of retrofits. Most of this volume, the study points out, would be captured by third-party suppliers like AMS Spectral UV, eltosch grafix, and IST Metz (parent of IST America).
Helping to encourage these sales is the fact that legacy press owners can expect the same results from their LED-UV retrofits as buyers of new presses will get from their integral systems.
No Age Discrimination Here
“The efficiency is exactly the same,” Jenkins says, adding that while an old press is neither as fast nor as automated as a new one, those comparative shortcomings won’t penalize the LED-UV retrofit to any degree. Printers who update vintage presses in this way can expect to “massively increase throughput” on the equipment, according to Ulland.
Bonallo notes that because of the way the cylinder sections are configured, some presses make it easier to position the LED-UV array at an optimal distance relative to the substrate than others. But in most cases, he adds, that shouldn’t be a factor in terms of performance.
Whether on a brand-new press or a legacy machine, agrees Woloshyn, “we’re just curing inks and coatings.”

This is a close-up of a portion of the LEDs and optics that comprise a LUV 3 LED-UV module from IST Metz, which says the product provides the highest LED power to the substrate currently available in the market.
Like conventional UV, LED-UV belongs almost exclusively to sheetfed offset work: the PRIMIR study reported being aware of no LED-UV-curing web offset press installations in North America at the time of publication.
Jenkins, however, thinks the technology might appeal to printers who want to install heatset web offset presses without also having to make room for the long hot-air dryers presses of this type require. According to Ulland, LED-UV units above and below the web can do the same thing an oven does, yielding “massive energy savings” and conserving plant space at the same time.
But LED-UV for web offset faces obstacles as a business proposition, not least of which is the decline of web volumes in many commercial product categories.
Bonallo concedes that LED-UV curing for web offset is possible in theory, noting that it is well established in label and narrow-web flexo. But he points out that doing it effectively at the highest web offset speeds could become cost-prohibitive because of the price of the hardware required, and the higher cost of LED-UV-compatible inks and coatings. Woloshyn says that although his company has fielded some inquiries about LED-UV for newspaper and commercial web offset applications, these printers tend to conclude that “the ROI doesn’t make sense for them.”
Innovations from the Vendors
However, there’s been more than enough activity on the sheetfed side to drive vigorous R&D and new product development for that segment of the market. eltosch grafix, for example, has stepped up the capabilities of its technology with LED Powerline Focus, a sheetfed system that uses advanced optics to maintain correct exposure intensity at varying distances from the substrate. Woloshyn says this assures nearly distance-independent curing, even at high press speeds.
The bestsellers among AMS Spectral UV’s X-series LED-UV arrays for commercial sheetfed offset are XP 9 and XP 11, which Ulland describes as engineered for large printing formats and high press speeds. Newly joining them is XV, a cost-competitive system that Ulland contends will significantly decrease the price point of LED-UV for retrofits.
He adds that soon to come from AMS Spectral UV is Twin Beam LED, a compact LED module that doubles the LED-UV dosage (photons of light energy contacting the surface of the substrate) for the most demanding coating requirements at the highest press speeds.
According to Bonallo, LUV 3 (LED-UV Version 3) from IST Metz provides the highest LED power and dosage to the substrate currently available in the market. He says its optic design overcomes problems of distance that arise when installing an LED-UV array in the delivery of a sheetfed press, where the gripper bar assemblies come between the UV light source and the substrate.
IST Metz also offers a hot-swappable, universal power supply that makes it possible to run conventional UV, LED-UV, or a combination of the two within the same curing system.
Little Reason Not to Buy
Jenkins says the questions he hears most often from his consulting clients tell him that the vendors have more work to do when it comes to educating printers about their dual curing options.
“People see the letters UV and think they’re basically the same thing, but they’re not,” he comments.
But in Bonallo’s opinion, dwelling on the differences between conventional UV and LED-UV is less important than acknowledging the idea that one day, energy curing by both processes could replace traditional drying methods altogether. The original method remains well-entrenched, and the newer one, with further technical progress still ahead of it, has ample room to grow.
“As the technology continues to advance, and as different wavelengths and corresponding chemistries for inks, coatings, and adhesives are developed into practical applications, we believe UV curing will become the dominant process for dry inks and coatings across multiple press platforms, with LED-UV contributing to the trend,” Bonallo says.
That spells opportunity all around. Woloshyn predicts that LED-UV will continue to rise as a share of his company’s business, thanks to the efficiencies it makes possible on new and legacy presses alike.
And Ulland believes that as the advantages of the technology become apparent to printers everywhere, more and more of them will say, “There’s so little that I wouldn’t want to buy LED-UV for."

Patrick Henry is the director of Liberty or Death Communications. He is also a former Senior Editor at NAPCO Media and long time industry veteran.
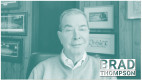




