Unfinished Symphony: The Evolving Definition of Post-Print Processing
This analysis was commissioned by Canon Solutions America, ESS and NAPCO Media to help printers better understand how today’s technology can optimize their production and how they can benefit by adopting these solutions.
The definition of “finishing” used to be simple: for folding cartons, it meant die cutting and gluing the boxes; for commercial and publication print, folding and binding the sheets. Today, “finishing” is a complex combination of basic and high-end processes taking place sequentially or simultaneously, often with verification that each step has been correctly performed.
The change in the meaning of finishing lies in what has happened to the definition of a saleable printed product. Folding, stitching, and other traditional processes still add value to printed sheets, but today’s customers also expect finishing to create one-of-a-kind, customized pieces for individual recipients.
This is why the repertoire of finishing now includes things like tracking codes, demographic enhancements and decorations, variable perforation, watermarks, and specialty coatings. They’re all aimed at encouraging a new generation of consumers to think of print as something more than what it once was perceived to be.
Business Model Evolution
The changed nature of finishing also drives change in the business model of printing and converting. Many printers are finding it difficult to maintain their profit margins just on the basis of print quality. Their customers take high-quality printed output for granted. As a result, there’s been steady appreciation in the value that finishing is seen to add.
This has consequences for the way the production chain operates. Until fairly recently, for example, the trade finishing business was an outsourced extension of printing: shops that provided basic services like trimming, folding, and stitching to print-only plants without finishing assets of their own.
Today, however, the portfolio of high-end services that trade finishers provide frequently determines what the end product is going to look like. In some projects, the finishing steps are so extensive that the printing may be the job’s smallest cost component.
When this is the case, the trade finisher may buy the printing and take a markup on that part of the job—a reversal of the traditional relationship. From the finishing end comes the combination of creative direction and the manufacturing know-how that ensures the printing can be finished as the customer requires.
Technology Advancements
Whether finishing takes place in trade shops or in vertically integrated printing plants, extreme technical sophistication is the hallmark of what it has become.
The process increasingly relies upon integrated production lines that can accept input from roll-fed and cut-sheet devices and, with the help of onboard inspection systems, verify that book blocks, covers, inserts, envelopes, and other components are correctly matched in error-free finished pieces—at full machine speed.
Today, computerized automation has brought speed, precision, and efficiency to finishing. A folder that used to take an hour to set up manually now can be made ready in minutes with the help of digital presets. This means there is less need for operators with traditional, hands-on mechanical qualifications—an important advantage for employers confronting a shrinking and deskilled labor pool.
A major change in late-model finishing systems is the accessibility of the technology that they provide. Because advanced technologies have migrated from high-end systems into mid-range solutions, users of these devices now can have finishing capabilities that were once out of their price range.
This changes investment expectations. A printer who buys a new, highly automated offset press to replace two or even three legacy presses wants to be able to make the same gain in productivity when purchasing new finishing equipment.
In conventional production, finishing processes such as varnishing, spot UV, and foiling take place either on press or on offline equipment. These proven analog methods are reliable for the kinds of high-volume jobs they are called upon to do, but they aren’t well suited to the quick-turnaround, short-run nature of digital printing.
This has prompted the digital press manufacturers to equip their devices with plug-and-play, electronic and mechanical interfaces that enable finishing systems to connect directly with print engines. Digital finishing and embellishment systems are built to keep up with, or stay reasonably close to, the output of the engines they support.
Finishing at GRAPH EXPO 2016
The progress of finishing technology was on full display at Graph Expo 2016, where show goers could see that what they used to think of as post-print processing means something very different today. Examples of finishing solutions promoted at Graph Expo included:
Duplo’s Digital Spot UV Coater uses inkjet and UV to apply an instantly curing gloss finish to defined areas of the printed substrate. A CCD camera recognition system ensures accurate application and alignment of the spot UV image on the sheet.
The OmniFold 3000 folder-gluer system from Kluge is designed to maximize converting throughput while minimizing set-up time. The system has a visual inspection system that checks for print quality, missing copy, and color quality on multiple substrates.
MGI’s iFOIL hot foil stamping system creates multicolored, variably printed metallic and embossing effects without films, dies, and conventional makeready. Running inline with MGI’s JETvarnish 3D digital spot UV coater, iFOIL brings digital enhancement to magazine covers, books, brochures, labels, and packaging one piece at a time or in thousands of copies.
The Presto II Digital saddle stitcher from Muller Martini has a modular feed system that lets it integrate easily with both digital and offset printing processes. The stitching components and the three-knife trimmer adjust automatically to product thickness, enabling each finished product to have a different thickness.
Designed to meet the growing demand for short-run die-cutting, the Standard Horizon RD-4055 Rotary Die Cutter can die-cut, crease, perforate, slit, hole punch, and round corner in one process for both digital and offset printed sheets. The system offers simplified changeover and operation through a color touchscreen.
Scodix builds a wide range high-end finishing capabilities into its Scodix S, Scodix Ultra, and Scodix E106 digital enhancement presses. Collectively called Scodix Sense, the finishing techniques include foiling, spot varnish, glitter, rainbow, tactile, and 3D holographic special effects.
Customer Expectations
What customers now expect of finishing solutions like these can be discerned in the practical questions they ask. Can we get our work done in one shift instead of two shifts with the help of a more efficient system? How can we help our veteran operators become more productive? How can we address the ergonomics of finishing tasks to reduce labor intensity? What can we do to combine and streamline multiple finishing steps into one process?
Customers want to take touches out of finishing. Where there are four separate finishing steps, for example, they want to see completion in one. Above all, customers want finishing equipment that they can readily integrate into whatever production workflows and MIS setups they already have in place. This means designing systems with truly open architectures to make integration seamless.
Folders and other finishing machines have to be able to process output from conventional, digital, and hybrid pressrooms. They have to accommodate a greater range of sheet sizes. Working in partnership with press manufacturers, finishing systems suppliers have adapted their product offerings accordingly.
One thing they recognize is that customers no longer perceive a difference between digital finishing quality and conventional finishing quality—the bar is set at the same height for both. In book production, for example, there can be no variation in binding performance between first-run copies printed on offset presses and backlist copies printed digitally on demand. Consistency is expected at every stage of the product life cycle.
Customers also want machine-generated proof that their finishing systems are operating without error and waste. Twenty years ago, a buyer of a folding carton gluer was content with a machine that could deposit the glue in the right spots on the form. Today that buyer expects a system equipped with cameras to verify the placement.
If the definition of finishing is not what it used to be, neither is the definition of its user base. This is partly because digital press manufacturers have been selling increasing numbers of systems to customers that do not belong to the mainstream printing industry.
These enterprise customers now have much more control over what and how much they print—and how they finish what they have printed. They want to be able to accomplish all printing and finishing steps in one process with a minimum of hands-on operation.
For this reason, user-friendly interfaces are high on their lists of must-have features. They know that with the help of an intuitive GUI, it can be easier to train non-printers to operate finishing equipment than it is to train veteran print employees who aren’t accustomed to computerized controls.
Ultimately, customers of all types rate finishing systems on quality, throughput, integratability, and ease of operation—not cost. They also prefer to deal with suppliers that offer a complete range of finishing solutions: one-stop sources they can call whenever they need a machine for a specific application.
- Companies:
- Canon Solutions America, ESS
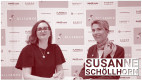




