Technifold has implemented a new, low-tech twist on the auto feeder that delivers the next best thing to an air-fed mechanism—all at a fraction of the cost.
The classic configuration of a friction feeder consists of a pair of rollers, usually rubber, one fixed and one turning which will separate and feed a small pile or stream of sheets into any number of printing or print finishing machines (see image 1). This means a tremendous amount of pressure is placed on a small surface area of the sheet at a single point of contact. The gap between rollers must be tight enough to prevent a double sheet, but with enough pressure to drive the sheet through this tight spot, which may require frequent adjustments.
- Categories:
- Finishing - Conventional
- Companies:
- Technifold USA

Trish Witkowski is Chief Folding Fanatic at the online community foldfactory.com. She holds a bachelor of fine arts degree in graphic design and a master of science degree in Graphic Arts Publishing from Rochester Institute of Technology's School of Printing Management and Sciences (now the School of Print Media).
An award-winning designer, Trish held the position of creative director for a Baltimore-based agency for six years, and has taught design and desktop publishing at the college level. She has a specialized expertise in the area of folding and is the creator of the FOLDRite™ system, a 2004 GATF InterTech™ Technology Award winner.
Trish frequently publishes articles for graphic arts industry publications, and has written three books on the topic of folding: A Field Guide to Folding, Folding for the Graphic Arts: A Teacher's Handbook, and FOLD: The Professional's Guide to Folding.



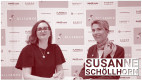

